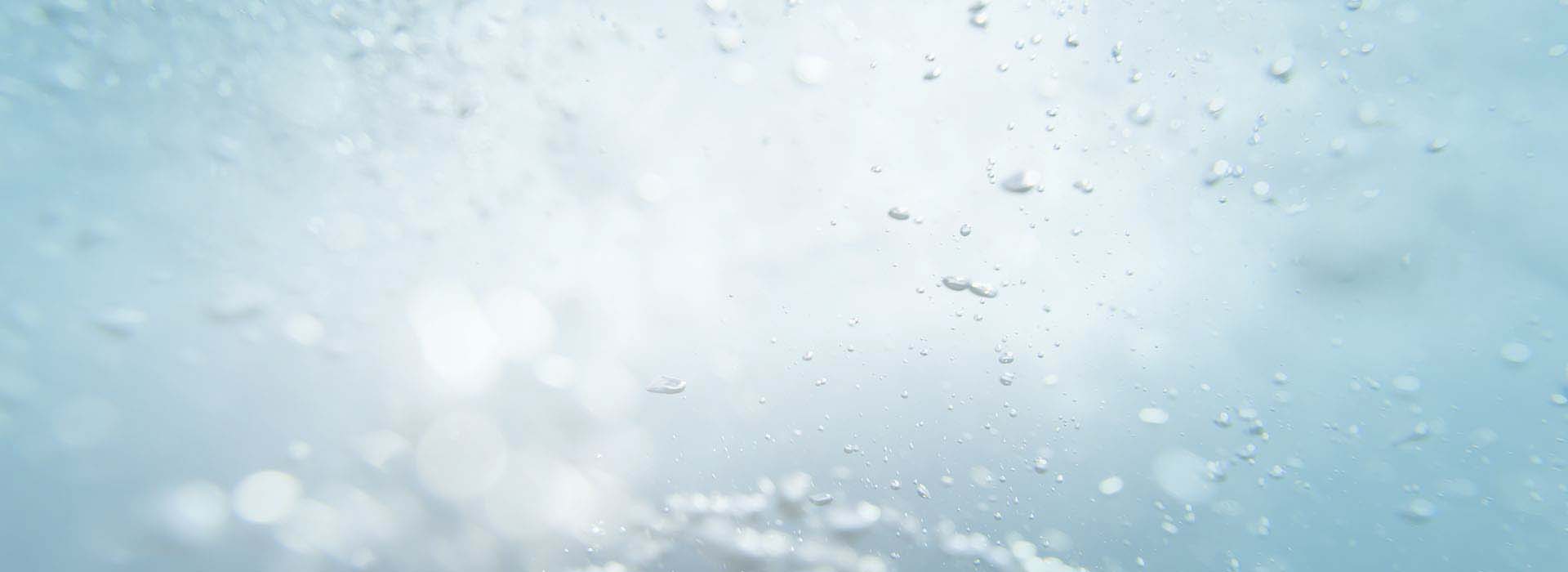
Treatment for salty process water
Proper process water treatment for every production
Large quantities of most salty process water are generated primarily in surface technology.
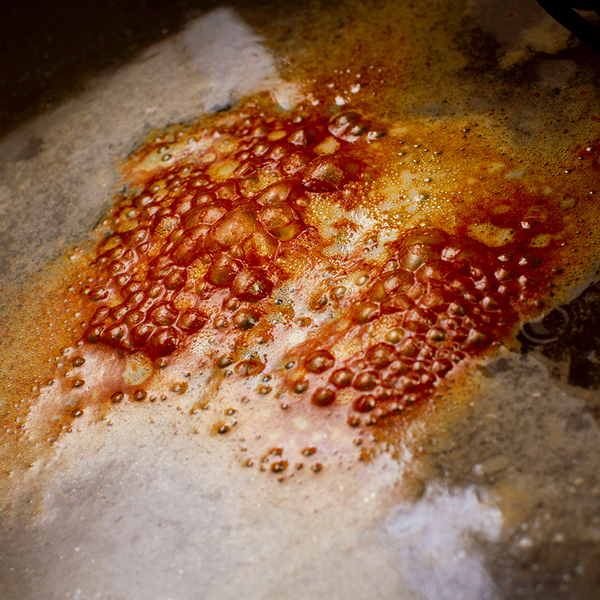
Frequent production steps here are pre-treatment and cleaning steps prior to surface finishing processes, such as corrosion protection processes or the application of coatings and paints. The qualitative requirements with regard to the rinsing steps integrated in the processes for pretreatment and surface finishing are now very high. The quality/purity of the rinsing water plays an eminently important role. High rinse water quality has a direct influence on the cleanliness of the surfaces to be cleaned. These must not show any residues before drying and the subsequent coating process. KMU LOFT Cleanwater can treat most of these salty process waters from the rinsing and active baths flexibly with an almost fully automatically customized KLC complete solution.
Process water treatment with KLC - a step ahead of the competition
Saline process water is often treated with a KLC forced circulation vacuum evaporator. This does not often require a full range of pre- and post-treatment steps. First, the various process waters would be collected from the rinsing and active baths. A pH adjustment may be necessary. The process water is treated safely and efficiently with a KLC forced circulation vacuum evaporator. The high distillate quality allows reuse in production. Salt and heavy metals contained in the process water are safely transferred into concentrate. The salt-containing concentrate can be further concentrated in a downstream process step, thus additionally saving disposal costs.
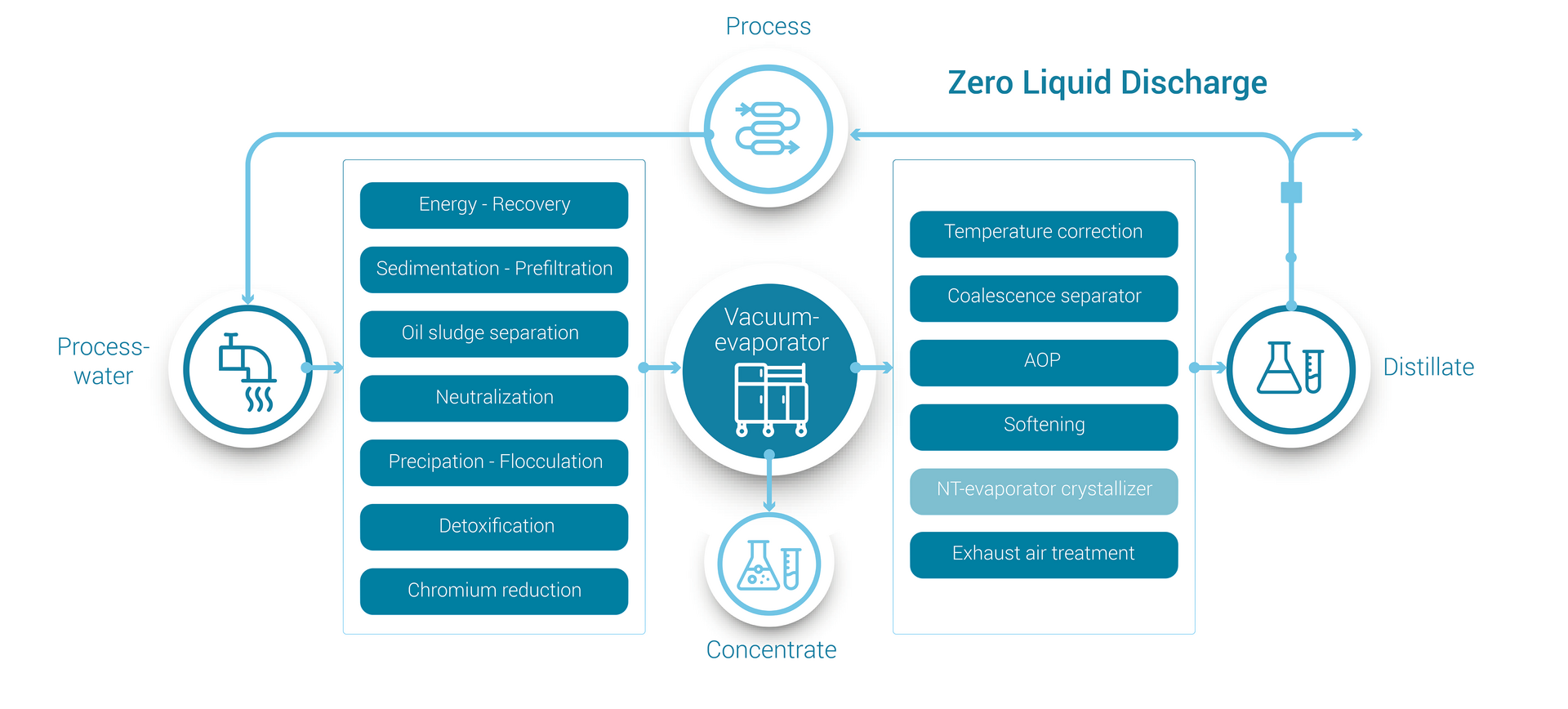
Benefit from the professional service of KMU LOFT Cleanwater
- Comprehensive consulting & process water analysis by the KLC competence team
- Process solution adapted to your special salty process water
- Reliable compliance with limit values, especially for pH, conductivity and heavy metals
- Detoxification of process water containing cadmium and chromium VI
- Significantly lower energy consumption compared to low-temperature evaporator technology
- Turnkey & space-saving complete system
- Low operating costs thanks to maximum energy efficiency
- Low disposal costs due to recirculation
- Low operating costs thanks to fully automatic operation
- User-friendly KLC machine control
- Industry 4.0 capable
The treatment of salty process water with a KLC solution is economical and sustainable.
Different methods for process water treatment of salty process water
Vibratory finishing
Vibratory finishing is a surface finishing process and is often used for deburring and polishing large bulk quantities. The process water produced consists mainly of the aqueous solution (compound) used with the abrasives to treat the workpiece.
In addition to abrasion, the salty process water is also contaminated with oily ingredients from previous process steps. Centrifuges are often used to extend the bath life, which often do not achieve the desired success. The use of a KLC vacuum evaporator extends the service lifetime of bath decisively, the purified distillate is returned to the bath circuit and saves fresh water additionally.
Electroplating
Electroplating technology or electroplating is an electrochemical process in which surfaces are coated with a metallic layer.
This method is used in the following industries:
- in the classical industries of metal working and processing
- in surface technology
- in the automotive and aerospace industry
- in microelectronics
The resulting process water contains complexing agents and heavy metals. By using the KLC vacuum evaporators in combination with a complete solution of pre- and post-treatment, these ingredients can be removed from the salty process water.
The limit values for zinc and nickel are complied with, and cadmium and chromium VI are safely detoxified.
Paint pretreatment/Surface technology
In surface technology, thorough cleaning is a prerequisite for an optimal result.
During the residue-free cleaning of the surface, salty process water is generated, such as from phosphating, passivation, pickling, anodizing/anodizing and electroplating.
The rinsing water quality is of decisive importance for the purity of the surface to be coated and subsequently for the quality of the subsequent surface coating.
Phosphating, iron phosphating, zinc phosphating
Phosphating is a surface engineering process. The production of a conversion layer is used for corrosion/wear protection or to improve paint adhesion. The process water produced before and after the iron or zinc phosphating process can be treated with a KLC vacuum evaporator.
The rinsing water quality is of decisive importance for the purity of the surface to be coated and subsequently for the quality of the subsequent surface coating.
Passivation
Passivation is a surface engineering process in which the metallic material is coated with a non-metallic protective layer, thus preventing oxygen corrosion. The rinsing water produced before and after the passivation process can be treated with a KLC vacuum evaporator.
The quality of the process water is of decisive importance for the quality of the surface and its subsequent coating.
Stainless steel pickling
Stainless steel pickling is a chemical surface engineering process. Pickling with hydrofluoric acid and nitric acid increases the corrosion resistance of the steel. Rinsing cycles are necessary before and after the pickling process. The resulting saline process water can be treated with a KLC vacuum evaporator.
Hardening plant
Hardening is used to increase the mechanical resistance of ferrous materials. This is achieved by heat treatment and rapid cooling (quenching) of the workpiece.
Salt water baths are frequently used as cooling media. They contain, among other things, nitrite- or nitrate-containing AS hardening salts.
After hardening, the workpieces are cleaned for the subsequent process steps. The salty process water can be cleaned with the help of the KLC vacuum evaporator. The hardening salts contained in the concentrate are reused. The almost salt-free distillate is recycled for the rinsing processes.
Tank and container cleaning
Used and residually emptied containers and threads are generated in all industrial sectors. After a rinsing process, they can ideally be reused or disposed of cleaned. These include transport containers, drums, reusable packaging and KLTs (small load carriers).
In addition to cleaning agents, the process waters also contain small amounts of all kinds of transport ingredients.
Salty process water can be treated cost-effectively and efficiently by means of the KLC vacuum evaporators. After process water treatment, it is returned to the rinsing cycle. This reduces the amount of concentrate to be disposed of to a minimum. Significant amounts of fresh water can be saved via this distillate reuse.
Washing and cleaning wastewater (salty)
In numerous sectors, washing and cleaning steps are necessary for the preparation of subsequent production steps.
These include the following industries:
A typical production step is the cleaning of parts after thermal or thermochemical heat treatment.
By using vacuum evaporator technology, washing and cleaning wastewater is treated safely and efficiently.
Reduced fresh water consumption via recirculation and distillate recycling and low energy costs of process water treatment have a positive effect on ongoing operating costs within the parts cleaning.
Radioactively contaminated wastewater
During the dismantling phase of a nuclear power plant, a large amount of weakly and moderately radioactively contaminated rinsing and cleaning water is generated. With the KLC vacuum evaporator, this contaminated process water can be reduced cost-effectively and efficiently.
The salt- and heavy metal-free, decontaminated distillate can be reused for rinsing and cleaning purposes. The small amount of radioactively contaminated concentrate is further conditioned for interim storage.
Recyclable water from recycling processes
Process waters containing precious metals derive from recycling processes in mines, refineries and surface operations. They often contain platinum, palladium, osmium, rhodium and gold.
The electroplating of plastics also produces process waters containing copper and nickel. Here, it is also worthwhile to recover the metals.
Landfill leachate
Landfill leachate is generated by precipitation and groundwater that seeps and drains through landfills. In the process, chemical compounds from the landfill material are dissolved in the water.
This process water is characterized by high levels of organic pollution and by contamination with water-soluble nitrates, sulfates, chlorides, and heavy metals.
These pollutant loads depend on various factors:
- the type of waste
- the weather conditions
- the biochemical degradation processes (decomposition) in the landfill site
Mine water
Mine water is formed by precipitation and groundwater seeping through various rock layers. In the process, the process water absorbs water-soluble mineral constituents.
Acid mine water is formed by the oxidation of pyrite, sulfur gravel, chalcopyrite and similar sulfides. Other constituents depend on the materials mined in the mine. In hard coal mining, for example, substances such as sodium chloride, nickel sulfate, iron oxides and manganese are produced.
Mine water is not only produced in active mines. It must also continue to be pumped out and treated in closed mines.